For mechanical engineering students, the most familiar thing is the lathe, and the lathe is divided into manual lathe and CNC lathe. Today, we will talk about what is a manual lathe.
What is a manual lathe
Ordinary lathe is a horizontal lathe that can process many types of workpieces such as shafts, disks, rings, etc. It is often used to process the internal and external rotary surfaces, end surfaces and various internal and external threads of workpieces, and it can be drilled, reamed, tapped and knurled by using the corresponding tools and accessories. General lathe is one of the most widely used lathes, accounting for about 65% of the total number of lathes, because its spindle is placed horizontally and is also known as horizontal lathe.
Structure and Function of Manual Lathe
The main components of a general lathe are: spindle box, feed box, slide box, tool holder, tailstock, light bar, screw and bed.
Spindle box: also known as the headstock box, its main task is the main motor from the rotary motion through a series of variable speed mechanism so that the spindle to get the required positive and negative two kinds of steering at different speeds, at the same time, the spindle box to separate some of the power will be transmitted to the movement of the feed box.
Feed box: also known as the tool box, the feed box is equipped with a feed movement of the variable-speed mechanism, adjust the variable-speed mechanism, you can get the required amount of feed or pitch, through the light bar or screw will be transmitted to the movement of the tool holder to carry out cutting.
Screw and light bar: Used to connect the feed box and slide box, and transfer the motion and power of the feed box to the slide box, so that the slide box can get the longitudinal linear motion. Screw is specifically used for turning a variety of threads and set up, in the workpiece into the other surface turning, only light bar, do not use the screw.
Slipper box: it is the manipulator box of lathe feeding movement, equipped with the mechanism to turn the rotary movement of light bar and screw into linear movement of tool holder, realizing the longitudinal feeding movement, transverse feeding movement and rapid movement of tool holder through the light bar transmission, and driving the tool holder to make the longitudinal linear movement through the screw in order to turn the threads.
Tool holder: the tool holder is composed of several layers of tool holders, its function is to clamp the tool, so that the tool for longitudinal, transverse or oblique feeding movement.
Tailstock: The rear center is installed for positioning support, and can also be installed with drills, reamers and other hole machining tools for hole machining.
Bed: The main parts of the lathe are installed on the bed, so that they maintain an accurate relative position when working.
Precautions in the operation of lathe
It is strictly prohibited for non-staff to operate the machine tool.
It is strictly prohibited to touch the tool, the rotating part of the machine tool or the rotating workpiece during operation.
Not allowed to use the emergency stop, such as in case of emergency with the button after stopping, should be in accordance with the machine tool before the start of the provisions of the re-check once again.
Not allowed to pedal the guide surface of the lathe, screw, light bar, etc., in addition to the provisions of the foot instead of hand-operated handle.
The inner wall has sand holes, shrinkage holes or keyway parts, not allowed to use the triangle scraper to cut the inner hole.
After pneumatic hydraulic chuck compressed air or liquid pressure must reach the prescribed value before use.
Turning long and thin workpieces, in front of the head of the bed on both sides of the extended length of more than 4 times the diameter, should be in accordance with the provisions of the process with the top. Center stand or follow the tool holder support. When extending behind the bed head, guards and warning signs should be added.
When cutting brittle metal or cutting is easy to splash (including grinding), protective stops should be added and the operator should wear protective glasses.
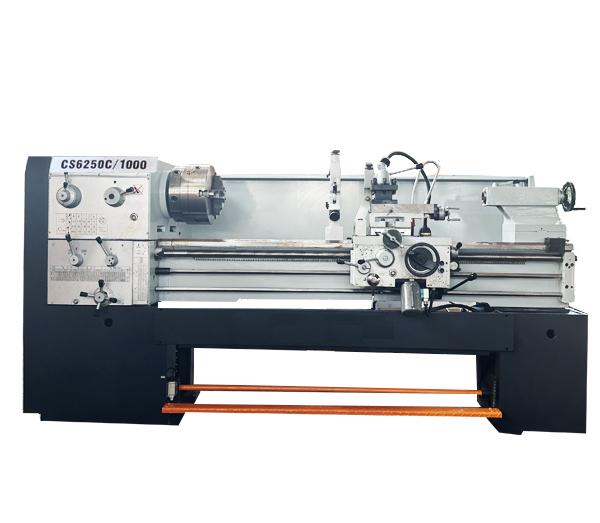